How Shipping Aggregates By Rail Works
Published on: April 27, 2024
Get an estimate for your project in 60 seconds

How Shipping Aggregates By Rail Works
In construction, aggregates—like sand, dirt, and gravel—are more than just raw materials. They form the backbone of our infrastructure. And while these might seem like simple materials, transporting them is anything but. This is where rail transportation, with its unique benefits, especially for large quantities, comes into play. At Hello Gravel we are experts in all things related to gravel and its transportation. With this article we are sharing our knowledge to help you navigate logistics for your project.
Key Takeaways:
- Aggregates, vital for infrastructure, require efficient transportation, and railways offer an optimal solution.
- Railcars vary in types:
- Hopper Cars: Best for easy unloading.
- Gondola Cars: Ideal for bulk materials.
- Boxcars: Protect aggregates from weather.
- Loading precision is key to avoid safety risks and optimize shipping costs.
- Rail shipping benefits:
- Economic: Reduced costs due to large carrying capacity.
- Eco-friendly: Lower emissions and land footprint.
- Safety: Fewer accidents compared to road transport.
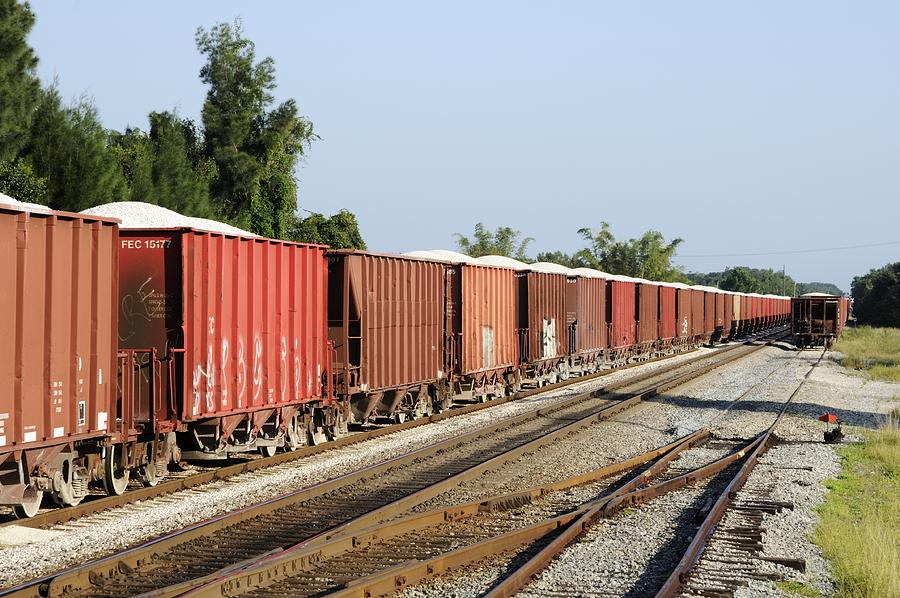
The transportation of aggregates by rail has seen a notable increase over the years. For instance, a decade ago, the rail-transported construction materials (including aggregates and cement) totaled 2.70 billion net tonne kilometers (tkm), which increased to 4.34 tkm by the end of 2017 according to the Office of Rail and Road (ORR). In 2023, there continues to be a steady flow of aggregates transported by rail.
From Quarry to Railcar
Long before aggregates see the inside of a railcar, they undergo a rigorous process at the quarry. Large excavators delve deep into the earth to extract them. Once out, they’re screened for size. This ensures that there’s no mix-up of large boulders with finer particles—a crucial step for any construction project. And, of course, washing comes next. This ensures any dust or contaminants clinging to the aggregates are removed. Then, it’s all about stockpiling them, waiting for the right railcar to transport them to their final destination.
Loading the Railcar
Hopper Cars
These are the go-to for most aggregate shipping. Built for effortless unloading, they come equipped with gates at the bottom. When these gates are opened, the aggregates simply pour out, minimizing manual labor and making the process swift. The hopper design facilitates a clean drop, reducing the chance of materials being stuck inside.
Gondola Cars
Think of these as the open baskets of the rail world. They’re essentially open-top cars that come in handy for bulk materials that don’t necessarily need protection from the elements. Their design makes them versatile, capable of holding various types of aggregates without the need for specialized loading or unloading equipment. Modern aggregate railway gondolas are designed with a length of 42 feet and have a capacity of up to 115 tons. These gondola cars support the movement of both phosphate and aggregates, with the newest cars being rated at 286,000 gross pounds when loaded. This design adheres to the heavy axle North American standard, illustrating the industry’s commitment to optimizing rail transport for aggregate materials
Boxcars
These are like mobile storage units. They’re mainly used when the aggregate materials need shielding from environmental factors, like extreme weather conditions. Prolonged exposure to rain, for instance, might compromise the quality of some aggregates. Boxcars, being fully enclosed, offer this protection.
The precision in the loading process can’t be stressed enough. There’s a fine balance to strike. Load too much, and you face potential safety hazards, from imbalances to spillages. Load too little, and you’re not making the most of your shipping expenditure.
The loading process must be exact. An overload can result in imbalances, spillages, and safety risks, while under-loading means not optimizing the shipping cost.
Once you have your railcars loaded and ready to go, you can’t just set off without a plan. This is where meticulous route planning comes into play.
The ideal route is not just the shortest, but the most efficient. Planners need to consider various factors:
Just like road traffic, rail traffic can lead to delays. It’s essential to choose routes that aren’t congested or have fewer scheduled trains. Regular track maintenance is vital for safe rail operations. Planners need to be aware of any ongoing or scheduled maintenance activities to avoid delays.Station Schedules are hubs of activity. Knowing the schedule helps in avoiding peak times and ensuring faster transit.
Trains maintain a lifeline with rail control centers. This continuous communication ensures they get real-time updates on any issues on the tracks ahead, ensuring not just their safety but also that of other trains sharing the tracks.
While a direct route from source to destination is always the preferred choice, it isn’t always possible. Sometimes, trains need to make intermediate stops. These stops could be for reasons like transferring aggregates to trucks for regions the rails don’t reach or offloading at distribution hubs for localized delivery.
Lastly, there’s a keen focus on safety. The rail authorities meticulously check the load, ensuring it’s secure. They also ensure all railcars are in peak mechanical condition, minimizing the chance of mishaps during the journey. This rigorous approach ensures that aggregates reach their destination in the same condition they were loaded, ensuring quality and safety throughout the transportation process.
Arrival and Efficient Unloading of Aggregates
Upon arrival, unloading begins, and time is of the essence:
Rotary car dumpers are high-tech mechanisms that can tip an entire car to unload aggregates swiftly. While, bottom dump unloading uses the natural force of gravity, allowing for a quick and even unload. Conveyor systems are specially beneficial for large-scale operations, these systems can quickly move aggregates to their next destination.
Why Rail? The Undeniable Benefits for Gravel Transport
Rail shipping is not just a matter of convenience; it’s often a strategic choice. Some notable benefits are:
Economic Efficiency
Trains can carry the equivalent load of hundreds of trucks, translating to substantial cost savings. One of the primary economic advantages of rail transport is its sheer volume capacity. A single train, depending on its configuration, can transport the equivalent load of hundreds, sometimes even thousands, of trucks. This isn’t just about moving more at once; it’s about cost per unit. When you spread the cost of operation over such a massive amount of cargo, the cost per ton or per item becomes significantly lower.
Trucks need fuel, maintenance, and drivers. Multiple that by hundreds, and the costs add up quickly. A train, on the other hand, runs on a singular continuous system. It uses fewer resources and manpower in comparison to its capacity, which translates into operational savings.
Trucks, due to their weight and number, can cause substantial wear and tear on our road systems. Maintenance and repair of roads can cost taxpayers billions. In contrast, railways have a longer lifespan and generally require less frequent maintenance.
Recently, Vulcan has initiated the linking of its aggregates resources with processing plants using rail transport lines in Southern California, which is one of the largest per-capita aggregate consumption regions in the U.S. This development is a testament to the growing recognition of rail transport’s efficiency in handling bulk materials like aggregates
Sustainability
With lower emissions, trains are an eco-friendlier choice. One of the most significant sustainable advantages of rail is its efficiency in emissions. Per ton-mile, trains emit considerably fewer greenhouse gases compared to trucks. This efficiency doesn’t only stem from the sheer volume they carry but also from the way trains are designed to move, using less energy for more cargo.
Railways, once established, use a fixed and narrow piece of land. Compare this to highways and roads, which can sprawl out and take up vast amounts of space. This land efficiency means less habitat disruption and more space for nature. The rail industry is continuously looking for cleaner and more efficient fuel solutions. From electrification to hydrogen fuel cells, the potential for an even greener rail future is on the horizon.
Safety
Fewer accidents occur with rail transport when compared on a per ton-mile basis to road transport. Railways operate in a highly controlled environment. Trains move on designated tracks, eliminating the uncertainties that come with road traffic, such as pedestrians, cyclists, and other drivers. When accidents involving trains occur, they’re often less frequent than truck accidents. The design of railways, combined with advanced signaling systems, minimizes the risk of collisions.Trains, by their nature, are designed to be stable. The risks of overturning or veering off course are minimal compared to trucks, which can be affected by various factors, from road conditions to weather.
Railways and trains undergo rigorous and regular inspections to ensure they are in optimal condition. This proactive approach is crucial in preempting potential issues and ensuring the safe transport of aggregates. At this time, Hello Gravel does not utilize trains to transport gravel or other aggregates.
If you’re looking for more information about hauling aggregates by rail click here.
Author: alan